Safety Procedures: A Procedure is not an Isolated Document
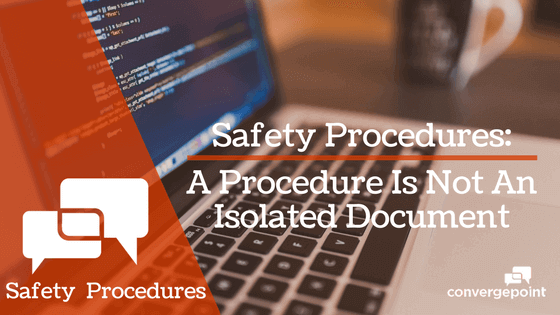
Safety Procedures: A Procedure Is Not An Isolated Document
Procedures are the bedrock of health and safety management. It could be said that they are the system at work. They come in many forms (if you pardon the pun) and with a dizzying variety of different names. They can be referred to as ‘works instructions’, ‘directives,’ ‘company directives’ and, more commonly, ‘standard operating procedures’ (SOPs). Just to really add to the naming diversity (read: confusion) some companies call their procedures ‘company policies’ or even simply ‘policies’. Whoever said that safety management was straightforward?
For the sake of clarity here, a procedure will be referred to as any company document that provides clear guidance in the form of written instructions on routines specific to a given operation or activity. There should be a procedure for any operation or activity that may pose a potential risk to the health and safety of employees. The purpose of a procedure is to ensure that the prescribed work is undertaken in a specific manner by achieving uniformity of performance. The end purpose is of ensuring that work is done as safely as possible – every time.
However, there is a worrying tendency in many companies for procedures to be written and applied on an ad-hoc, as-needed basis, almost as if in a systemic vacuum. This runs completely contrary to the fundamental principle of any documentation system, namely that all documents should be interconnected with all other related documents in a given system. This principle acknowledges that documentation should be systemically relevant. It also acknowledges that cross-referencing of documentation is vitally important for verification purposes. As any management system auditor will assert, the verifiability of documentation is central to any management system audit. That is why safety auditors are so demanding about the ability to cross-verify different documents within a given management system. It is what could be called the ‘golden thread’ that should run through all documentation systems. Without it, documents hang like loose threads.
An example of this golden thread could be thus: a procedure pertaining to the safety requirements when using a welding machine could in turn be intrinsically linked to documentation relating to occupational health (a procedure on periodic medical testing that is required for all welders) to industrial hygiene (indoor air quality monitoring assessments at welding bays in a workshop) to training (training needs matrices regarding induction, basic safety awareness and welding-specific technical training for welders) to any other documentation relevant to how welders can conduct their work in a safe and healthy manner. ‘Documentation’ here is clearly as diverse as the very name implies. It is when all these divergent yet related documents are able to confer with one another that one has attained a mature and valuable documentation system.
Yet safety teams and certain divisions see fit to write procedures that, however well written and risk-relevant, are not suitably related to other documentation or even other divisions in the same company. This so-called ‘island syndrome’ in the writing of procedures undermines their efficacy. It also undermines the ability to verify such documentation within a system. It might even make enforcement of these alone-standing procedures more difficult.
If no man is an island (especially in safety management), then neither should any procedure be ‘an island’. That is why it is so important that safety procedures be an integrated part of a given safety documentation system. Only then can they be considered relevant, fully enforceable and verifiable.