Safety Procedures: The Essentials of Industrial Hygiene Risk
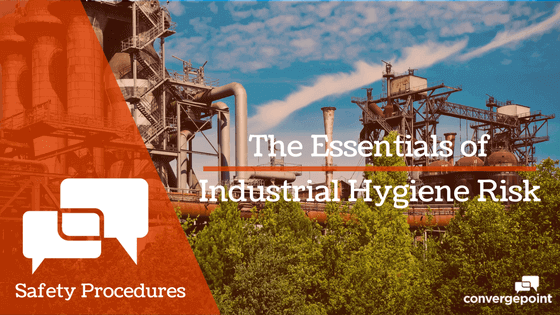
Safety Procedures: The Essentials of Industrial Hygiene Risk
Industrial hygiene (also referred to as occupational hygiene in some other countries) is “the science of protecting and enhancing the health and safety of people at work and in their communities”, as according to the American Board of Industrial Hygiene (ABIH). To be brutally frank, that definition by the ABIH is the very epitome of a definition at its most broad, most vague and frankly lazy. For the sake of this article (and greater clarity) industrial hygiene can be considered the identification and control of those factors in the workplace that may cause ill-health to employees and those in the community.
Let it be clear: industrial hygiene is primarily a matter relating to occupational and community/public health, with safety merely allied by inevitable association rather than its central focus. That may explain why so many safety practitioners are decidedly uncomfortable with the management of risks due to industrial hygiene factors in their OSH system. This short article aims to provide an overview of some essentials regarding risks pertaining to this often complex and technical discipline.
Central to understanding industrial hygiene risk is to focus foremost on the hazards thereof. Once one understands hygiene hazards in the workplace, the rest follows. In context, those factors that may cause ill-health are de facto hazards. These factors are most correctly referred to as ‘stressors’ given that they cause stress on the human body and mind. There are five main categories of stressors, namely: chemical (like benzene or hydrochloric acid), physical (with noise or temperature as examples), biological (examples being grain dust or bacteria), ergonomic (as with poor posture or repetitive motions) and psycho-social (e.g. stress or bullying in the workplace).
To better understand the most pertinent essentials of industrial hygiene, one does well to know what are referred to as the ‘four stages’ of industrial hygiene. These stages are based on the (1) anticipation, (2) identification, (3) evaluation and (4) control of stressors that may cause ill-health in the workplace or to the community. Let us consider these stages using a physical stressor such as radiation by way of example: you ‘anticipate’ the radiation by understanding your processes and knowing that radiation may be emitted at certain parts of your plant. You then identify precisely where said radiation may be emitted and how so, etc. You then evaluate the stressor by having levels of radiation tested where so needed. Only then can proper controls be implemented in order to minimize levels of radiation to which workers and even the local community may be exposed. And that is industrial hygiene in a nutshell.
With the above in mind, it should be clear to any practitioner that risk assessments will naturally follow from these stressors (read: hazards). And they will do so far more comprehensively if said stressors have been properly anticipated, identified, evaluated and controlled. Any risk assessment that flows from so thorough an understanding of industrial hygiene factors will be meaningful and, more importantly, valid. Hygiene factors should also be instrumental when recording, investigating, reporting, costing and recalling any health-related illness, disease or death. After all, more often than not it is an industrial hygiene stressor that will have been a contributing (if not primary) causation of illness, disease or death.
Safety management cannot wish industrial hygiene factors away from any workplace. Nor can it simply dump them on the occupational health practitioner. An unhealthy workplace quickly becomes an unsafe workplace. Industrial hygiene is a pivotal cornerstone of any OSH system that must be understood. Can you in good conscience think otherwise?