Safety Training: The Systems Guru Known as Deming
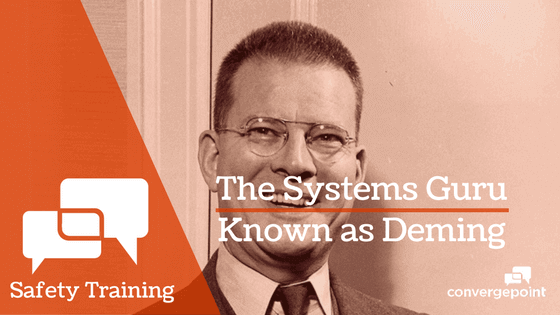
Safety Training: The Systems Guru Known As Deming
PDCA – Plan, Do, Check, Act. That is an acronym and those are words with which any safety manager or professional should be well-acquainted. In fact, the PDCA cycle should be at the heart of any management system, be it for finance, sales, logistics, IT, OSH, EHS or any other system that needs to be organized and structured. In-built with continuous improvement, it is its sheer simplicity that is the beauty of the PDCA cycle.
Enter Dr. W. Edwards Deming. There is a reason why the PDCA cycle is often called the Deming Cycle. A statistician by trade, Deming became something of an icon in Japan due to his management-related consulting work there in the post-World War II reconstruction period. His forte was particularly in the field of quality management and he quickly became a renowned author and expert on management system theory. For Deming, a system without planning, implementation, checking and corrective actions and proper review was a system doomed to failure.
At that time, systems theory was still nascent in industry and business. Deming could be considered a visionary, as he was a great believer that when things didn’t work in an organisation it was not the worker that was at fault (the prevailing belief by most owners and management then), but that the organization’s management system itself was to blame. This can only be considered revolutionary, as Deming believed that the seemingly abstract (i.e. the ‘invisible’ management system) and not the physical (i.e. the worker or machinery, etc) was where responsibility should be apportioned when things went wrong or did not work.
Deming was not only a great systems thinker but very adept at writing about systems in a concise, even catchy manner. This can be seen in his treatise titled “Seven Deadly Diseases”, which included such ‘ills’ in his mind such as an emphasis on short-term profits and management considered too mobile and inconstant. Management came under even closer scrutiny in his detailed list which he called “A Lesser Category of Obstacles”. Mistakes by management, according to Deming, included neglecting long-range planning, relying too much on technology to solve problems and commonly held excuses such as “our problems are different”.
Deming rightly put responsibility for and of management systems squarely where needed – on management. He scolded irresponsible or arrogant management teams for placing the blame on workforces (who are responsible for only 15% of mistakes) where it was in fact the incorrect or inadequate system desired by management that should be blamed (being usually responsible for 85% of unintended consequences, he argued). Although a convivial if shy man, Deming took no prisoners with statements like, “Learning is not compulsory… neither is survival”.
It is telling that Deming wasn’t even comfortable taking credit for the cycle. He would openly refer to it as the “Shewhart cycle”. This was in honour of Walter A. Shewhart, who was also a well-regarded statistician. It should be noted that Deming later modified PDCA to “Plan, Do, Study, Act” or ‘PDSA’. Whether it be PDCA, PDSA or any variation thereof, his influence on health and safety/EHS management cannot be underestimated.
It may have been initially developed for quality management by an American statistician to rebuild post-war Japanese industry, but the Deming Cycle continues to be synonymous with safety management that is well-planned, well-executed and that forces an organization to strive for continuous improvement at all times. As Deming stated, “A bad system will beat a good person every time”. How very true.
Photo Credit: The W. Edwards Deming Institute®