Safety Management System and Personal Protective Equipment
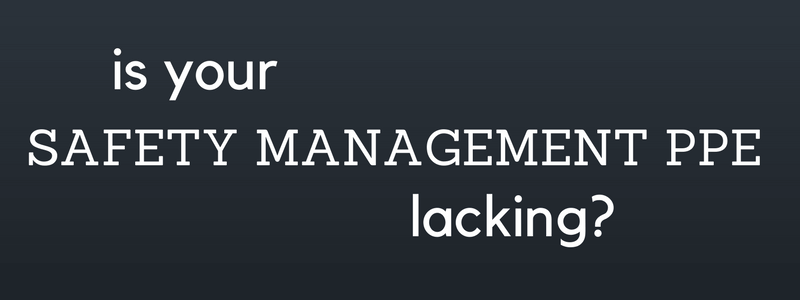
Safety Management System and Personal Protective Equipment
Personal protective equipment (PPE) could be considered the ‘fall guy’ of safety management. As any safety professional knows all too well, the dogma in risk management is that PPE is the absolute last resort as a control against a given hazard or risk. There may be variations between different hierarchies of authority, but without exception, the use of PPE should always be considered last. Be that as it may, it is contended here that PPE gets a bad rap and deserves its rightful place in the prevention of injuries and occupational disease.
PPE does have its place in safety management, of course. According to OSHA, PPE is “designed to protect workers from serious workplace injuries or illnesses resulting from contact with chemical, radiological, physical, electrical, mechanical, or other workplace hazards.” PPE is varied and can include face shields, safety glasses, hard hats, non-slip safety shoes, protective coveralls, gloves, and earplugs. OSHA’s primary PPE standards can be found in Title 29 of the Code of Federal Regulations (CFR), Part 1910 Subpart I, as well as similar regulations in those states with OSHA-approved state plans. Also relevant from a regulatory standpoint is OSHA’s Personal Protective Equipment Standard Compliance Directive (Directive Number: CPL 02-01-050) which came into effect in October 2011 and which is known informally as the PPE Guidelines for General Industry. It’s vital that you read them up if you haven’t already!
PPE Hazard Assessment
OSHA also insists that an organization undertake its own PPE Hazard Assessment, and which must include all necessary PPE considerations within a management system, particularly about the risk assessment process and the implementation of operational controls after that. Failure to do this would be an infringement of an organization’s safety and health due diligence, according to OSHA.
The statistics keep reminding us how PPE usage is often lacking. According to the Centers for Disease Control and Prevention, more than 1-million hospital emergency visits by workers in the U.S. could be avoided every year if only PPE had been worn. In 2009 alone, hand injuries cost American employers over 500-million dollars in lost time, claims, and the other costs typical of occupational injuries. That is why it so important that PPE be part of a formal incident reporting system such as ConvergePoint – the failure to use appropriate PPE is not only a system non-conformance but should even be recorded as a near miss.
Personal Protection Equipment Usage
There are specific tasks and workplaces that not only necessitate PPE usage, they demand it. Talk to any radiation protection officer or worker, and they will quickly confirm that PPE is an essential control for their work with radiative material or equipment. Their respirators and radiation monitoring devices/badges are not ‘nice-to-haves’ but essential for their health. Ditto the worker who handles acids. The key words here are ‘pure hazards.’ Pure hazards like radiation, acids and specific explosive materials are those that are inherently dangerous, i.e., they do not require other hazards or hazardous conditions to make them hazardous. Once again, any safety professional worth their salt knows this well.
The crux of the matter, however, is not the importance of PPE about pure hazards or as an important yet ultimately final control. The true importance of PPE relates to those more than one million American workers who land up in the hospital each year due to not having worn the correct PPE. That statistic alone proves that PPE’s reputation as the ‘poor cousin’ in safety management is not only problematic but dangerous. That statistic suggests a lack of worker awareness or understanding of the actual risks in their work, not to mention a failure in risk assessment. It even denotes a woeful lack of safety management by employers.
Productive Safety Management
PPE cannot be king and master in the workplace. That is lazy safety management. However, nor can it continue to be the devalued ‘underling’ in the hierarchy if safety and healthy controls. Ultimately, the logic that PPE should always be the last resort may not be doing American workplace safety or workers any favors.
ConvergePoint
Our comprehensive safety management software solutions can help you to track every step of attaining or assessing competency. Operating on one secure SharePoint portal using templates built on industry best practices, the actions of your team can be managed through role-based access permissions. A detailed version history page provides a real-time record of version changes that supports every element of policy workflow from creation to ongoing management and revision.
The opportunity to move your manual systems to the next level is closer than you may think. To learn more about our software now available on SharePoint On-Premise,SharePoint Online via Office 365, and as a Software-as-a-Service, ,schedule a demo now.